Rotary Table Speeds Production
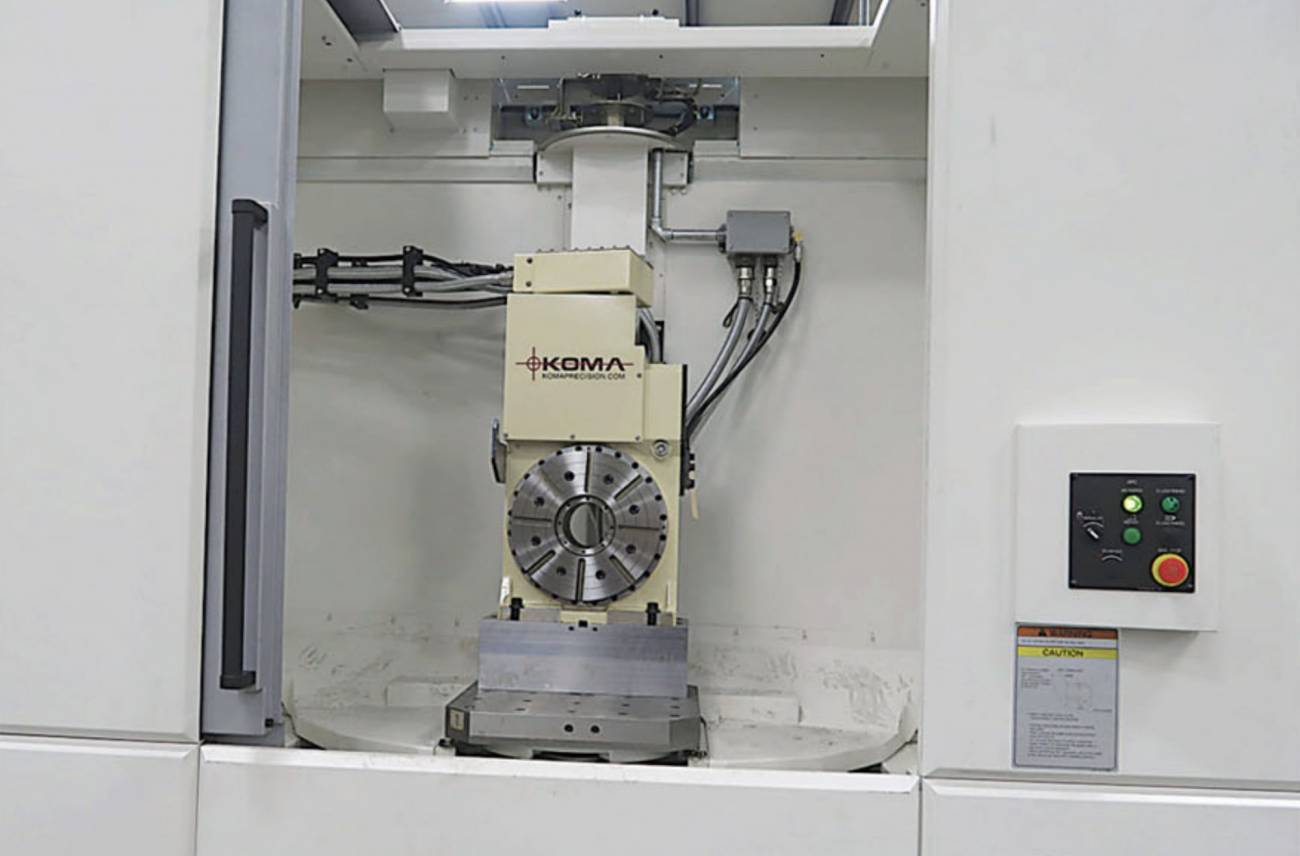
Having two pallets on the HMC increases our efficiency and time management. The operator is more flexible as to when he can load/unload the part. Plus, the machine is not waiting on the load/unload.
- Don Moody, Precise Machining & ManufacturingCompanies have a variety of machine configurations to choose from when looking to process a multiple-sided part. In the quest to squeeze costs, parts manufacturers realize that reducing setup time and machine downtime can often make or break a job.
One solution is the addition of a rotary table to a horizontal machining center so it has 5-axis capability. Depending on the machine control, this configuration can turn a standard 4-axis machining center into a 4+1 or simultaneous 5-axis machine tool. The addition of a rotary table utilizes all of the advantages of an HMC, including automatic pallet changing, enhanced chip evacuation and decreased setup times, while seamlessly adding an extra axis.
Precise Machining & Manufacturing LLC has been machining complex aerospace parts at its Tulsa, Okla., facility since 1974. The company has worked on major programs for customers such as Boeing, Spirit Aerosystems and the Triumph Group.
When Precise was looking for a 5-axis solution, it selected a Tsudakoma 12” (304.8mm) Model RBA-320K from Koma Precision Inc., East Windsor, Conn., for its Okuma HMC. In explaining Precise’s choice, Engineering Manager Don Moody said adding a rotary table costs much less than a dedicated 5-axis machine. “It also allows us to get to the center of the part easier.”
Unlike a full 5-axis, trunnion-style machine, an HMC plus rotary table allows setting up parts on the pallet outside the machining area while parts loaded on a second pallet are being machined. This drastically reduces downtime caused by stopping the machine to set up the fixture. The spindle utilization of an HMC can often be more than twice as much as that of a vertical machining center.
“Having two pallets on the HMC increases our efficiency and time management,” Moody said. “The operator is more flexible as to when he can load/unload the part. Plus, the machine is not waiting on the load/unload.”
To maintain the automatic pallet changing capabilities of the HMC, Koma’s Integration Division installed a cable management system onsite. it allows the rotary table to remain connected throughout a pallet change while keeping all the cabling out of the way of fixtures and metal chips. Furthermore, if there are hydraulics or air-sensing lines involved, this system can monitor and actuate automatic fixturing.
Cable management is accomplished with a scissor arm above the pallet that rotates or bends along with the movement of the B-axis on the HMC. On top of the rotary table, a swivel box permits the pallet to rotate ±120° in a standard configuration.
When machining high-quality aerospace parts, high rigidity and positioning repeatability are key. In this case, the Tsudakoma RBA-320K was a good fit because of its hydraulic dual-disc clamping system. This system maintains the fixture and part positioning while the machining center is taking its cuts. The machine is only as accurate as the rotary table, so positioning repeatability throughout the entire production run is critical to making good parts.
Moody confirmed the benefits of a rotary table setup. “We have many Tusdakoma rotary tables, and they all perform very efficiently and reliably. We run them day in and day out, 24/7.”